Tipos de remaches
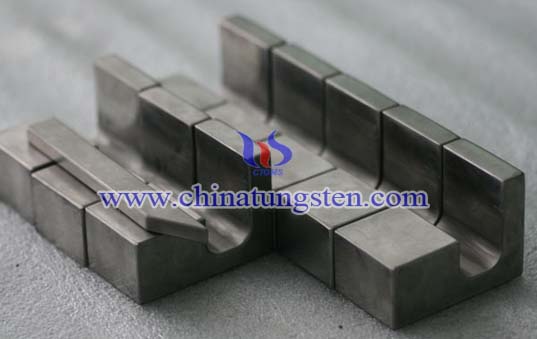
Hay varios tipos de remaches, diseñados para satisfacer diferentes requisitos de costo, accesibilidad y resistencia:
1) barra de rivetsbucking sólido
Los remaches sólidos son uno de los tipos de sujetadores más antiguos y confiables, y se han encontrado en hallazgos arqueológicos que datan de la Edad del Bronce. Los remaches sólidos consisten simplemente en un eje y una cabeza que se deforman con un martillo o una pistola de remaches. Los remaches sólidos se utilizan en aplicaciones donde la confiabilidad y la seguridad son importantes. Una aplicación típica para remaches sólidos se puede encontrar dentro de las partes estructurales de las aeronaves.
2) barra de rivetsbucking semi-tubular
Los remaches semitubulares (también conocidos como remaches tubulares) son similares a los remaches sólidos, excepto que tienen un orificio parcial (opuesto a la cabeza) en la punta. El propósito de este orificio es reducir la cantidad de fuerza necesaria para la aplicación al enrollar la parte tubular hacia afuera.
3) Remaches ciegos
Los remaches ciegos son tubulares y se suministran con un mandril a través del centro. El ensamblaje del remache se inserta en un orificio perforado a través de las piezas que se unirán y se utiliza una herramienta especialmente diseñada para introducir el mandril en el remache. A diferencia de los remaches sólidos, los remaches ciegos se pueden insertar e instalar completamente en una junta desde solo un lado de una parte o estructura, "ciegos" al lado opuesto.
4) Remaches de unidad
Un remache de impulsión es una forma de remache ciego que tiene un mandril corto que sobresale de la cabeza que se introduce con un martillo para abrir el extremo insertado en el orificio.
También se pueden usar con plástico, metal y otros materiales y no requieren una herramienta de ajuste especial que no sea un martillo y posiblemente un bloque de respaldo (acero o algún otro material denso) que se coloque detrás de la ubicación del remache al martillarlo. lugar. Los remaches impulsores tienen menos fuerza de sujeción que la mayoría de los otros remaches.
5) Remaches a ras
Un remache al ras se usa principalmente en superficies metálicas externas donde la buena apariencia y la eliminación de la resistencia aerodinámica innecesaria son importantes. Un remache al ras se aprovecha de un orificio de avellanado, también se les conoce comúnmente como remaches avellanados. Los remaches avellanados o empotrados se utilizan ampliamente en el exterior de las aeronaves por razones aerodinámicas. Se puede realizar un mecanizado adicional posterior a la instalación para perfeccionar el flujo de aire.
6) Remaches pop
Los remaches pop tienen un uso limitado en aviones y nunca se usan para reparaciones estructurales. Sin embargo, son útiles para la alineación temporal de agujeros. Además, algunos aviones "construidos en casa" utilizan remaches Pop. Están disponibles en cabeza plana, cabeza avellanada y cabezales de descarga modificados con diámetros estándar de 1/8, 5/32 y 3/16 pulgadas. Los remaches pop están hechos de aleación de aluminio suave, acero, cobre y Monel.
7) Remaches de bloqueo de fricción
Una de las primeras formas de remache ciego que fue la primera en usarse ampliamente para la construcción y reparación de aeronaves fue el remache de bloqueo por fricción Cherry. Originalmente, los bloqueos de fricción de Cherry estaban disponibles en dos estilos, con orificio de vástago hueco y tipos de auto-enchufes.
Los remaches de bloqueo por fricción de Cherry están disponibles en dos estilos de cabezal, universal y de 100 grados avellanados. Además, generalmente se suministran en tres diámetros estándar, 1/8, 5/32 y 3/16 pulgadas.
8) Remaches autoperforantes
Self-Pierce Riveting (SPR) es un proceso de unión de dos o más materiales con un remache de ingeniería. A diferencia de los remaches sólidos, los remaches pop y los remaches semi-tubulares, los remaches autoperforantes no requieren un orificio perforado o perforado.
El remache autoperforante perfora completamente el (los) material (es) de la hoja superior, pero solo perfora parcialmente la hoja inferior. Como el extremo trasero del remache no se rompe a través de la lámina inferior, proporciona una junta estanca al agua o al gas. Con la influencia del troquel molesto, el extremo de la cola del remache se ensancha y se bloquea en la hoja inferior formando un botón de perfil bajo.
Para resumir, los remaches deben ser más duros que los materiales que se unen, se tratan térmicamente a varios niveles de dureza, dependiendo de la ductilidad y dureza de los materiales. Los remaches vienen en una gama de diámetros y longitudes dependiendo de los materiales que se unen, los estilos de cabezas son avellanado al ras o cabezas de plato.
Los sistemas de remachado pueden ser manuales o automatizados, dependiendo de los requisitos de la aplicación, todos los sistemas son muy flexibles en términos de diseño del producto y facilidad de integración en un proceso de fabricación.