Rivet Types
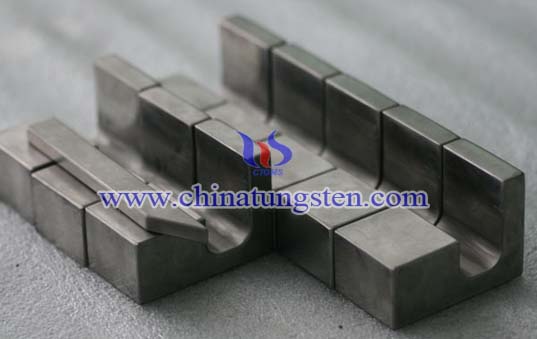
There are a number of types of rivets, designed to meet different cost, accessibility, and strength requirements:
1)Solid rivetsbucking bar
Solid rivets are one of the oldest and most reliable types of fasteners, having been found in archaeological findings dating back to the Bronze Age. Solid rivets consist simply of a shaft and head which are deformed with a hammer or rivet gun.Solid rivets are used in applications where reliability and safety count. A typical application for solid rivets can be found within the structural parts of aircraft.
2)Semi-tubular rivetsbucking bar
Semi-tubular rivets (also known as tubular rivets) are similar to solid rivets, except they have a partial hole (opposite the head) at the tip. The purpose of this hole is to reduce the amount of force needed for application by rolling the tubular portion outward.
3)Blind rivets
Blind rivets are tubular and are supplied with a mandrel through the center. The rivet assembly is inserted into a hole drilled through the parts to be joined and a specially designed tool used to draw the mandrel into the rivet. Unlike solid rivets, blind rivets can be inserted and fully installed in a joint from only one side of a part or structure, "blind" to the opposite side.
4)Drive rivets
A drive rivet is a form of blind rivet that has a short mandrel protruding from the head that is driven in with a hammer to flare out the end inserted in the hole.
They can also be used with plastic, metal, and other materials and require no special setting tool other than a hammer and possibly a backing block (steel or some other dense material) placed behind the location of the rivet while hammering it into place. Drive rivets have less clamping force than most other rivets.
5)Flush rivets
A flush rivet is used primarily on external metal surfaces where good appearance and the elimination of unnecessary aerodynamic drag are important. A flush rivet takes advantage of a countersink hole, they are also commonly referred to as countersunk rivets. Countersunk or flush rivets are used extensively on the exterior of aircraft for aerodynamic reasons. Additional post-installation machining may be performed to perfect the airflow.
6)Pop rivets
Pop rivets have limited use on aircraft and are never used for structural repairs. However, they are useful for temporary lining up holes. In addition, some "home built" aircraft utilize Pop rivets. They are available in flat head, countersunk head, and modified flush heads with standard diameters of 1/8, 5/32 and 3/16 inch. Pop rivets are made from soft aluminum alloy, steel, copper, and Monel.
7)Friction-lock rivets
One early form of blind rivet that was the first to be widely used for aircraft construction and repair was the Cherry friction-lock rivet. Originally, Cherry friction-locks were available in two styles, hollow shank pull-through and self-plugging types.
Cherry friction-lock rivets are available in two head styles, universal and 100 degree countersunk. Furthermore, they are usually supplied in three standard diameters, 1/8, 5/32 and 3/16 inch.
8)Self-Pierce Rivets
Self-Pierce Riveting (SPR) is a process of joining two or more materials using an engineered rivet. Unlike solid rivets, pop rivets and semi-tubular rivets, self-pierce rivets do not require a drilled or punched hole.
The self-pierce rivet fully pierces the top sheet material(s) but only partially pierces the bottom sheet. As the tail end of the rivet does not break through the bottom sheet it provides a water or gas tight joint. With the influence of the upsetting die, the tail end of the rivet flares and interlocks into the bottom sheet forming a low profile button.
To sum up, rivets need to be harder than the materials being joined, they are heat treated to various levels of hardness depending on the materials ductility and hardness. Rivets come in a range of diameters and lengths depending on the materials being joined, head styles are either flush countersunk or pan heads.
Riveting systems can be manual or automated depending on the application requirements, all systems are very flexible in terms of product design and ease of integration into a manufacturing process.